In the gold mining industry, the efficiency and productivity of a gold ore beneficiation production line largely depend on the proper selection and configuration of equipment. As a renowned factory dedicated to manufacturing top - notch mining equipment for crushing, screening, and mineral processing, we offer tailored solutions to maximize the value extraction from gold ores.
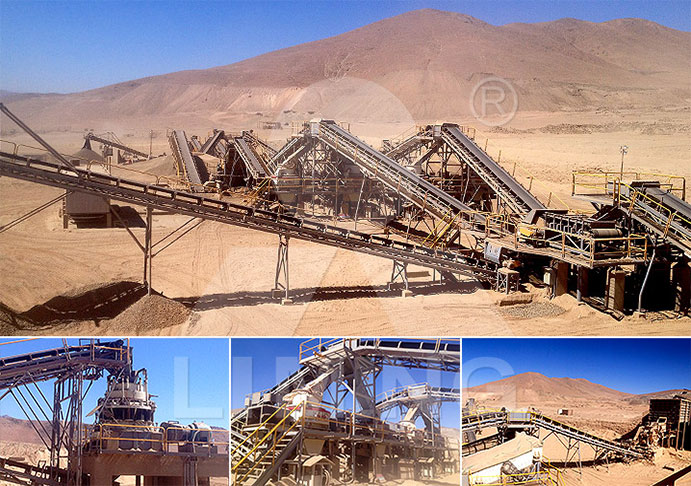
The Foundation: Key Equipment in Gold Ore Beneficiation Lines
Crushing Equipment
The initial stage of any gold ore beneficiation process is crushing, which reduces the size of the raw ore for subsequent processing. For coarse crushing, jaw crushers are the go - to choice. Their robust structure and high - crushing ratio can handle large - sized gold ores with ease. For example, when dealing with hard - rock gold ores, a heavy - duty jaw crusher can efficiently break down the material to a suitable size for secondary crushing.
For medium and fine crushing, cone crushers or impact crushers are commonly used. Cone crushers are ideal for producing a consistent product size, making them suitable for processing sulfide gold ores that require precise particle size control for further flotation or cyanidation processes. Impact crushers, on the other hand, are more effective for brittle gold ores, providing a high reduction ratio and good - shaped product particles.
Screening Equipment
After crushing, screening equipment plays a vital role in separating the crushed ore into different size fractions. Vibrating screens are widely applied due to their high screening efficiency and large processing capacity. They can accurately classify the ore, ensuring that only the appropriately sized particles move on to the next processing stage. For instance, in a placer gold deposit beneficiation line, vibrating screens can quickly separate the gold - bearing sand from larger pebbles and debris, improving the overall recovery rate of gold.
Mineral Processing Equipment
Flotation Machines: In the case of sulfide and refractory gold ores, flotation machines are essential. These machines use the principle of surface chemistry to selectively separate gold - bearing minerals from gangue. Modern flotation machines are designed with advanced aeration and mixing systems, which can enhance the flotation efficiency and increase the gold concentrate grade.
Cyanidation Tanks: For ores suitable for cyanidation, large - capacity cyanidation tanks are required. These tanks provide a sufficient reaction space for the gold to dissolve in the cyanide solution. Equipped with efficient agitation devices, they ensure uniform mixing and accelerate the gold dissolution process.
Equipment Configuration for Different Project Scales
Small - Scale Gold Mining Projects
Small - scale projects often have limited budgets and space. Compact and cost - effective equipment combinations are preferred. For example, a small - scale gold ore crushing system could consist of a small - sized jaw crusher followed by a hammer crusher for secondary crushing. A simple circular vibrating screen can be used for screening. In terms of mineral processing, a small - batch flotation machine or a simple cyanidation setup can be adopted, depending on the ore type. This configuration not only meets the basic production requirements but also reduces the initial investment cost.
Medium - to - Large - Scale Gold Mining Projects
These projects demand high - capacity and highly automated equipment. A multi - stage crushing system, such as a combination of jaw crushers, cone crushers, and vertical shaft impact crushers, can be employed to handle large volumes of raw ore efficiently. High - precision and large - area vibrating screens are necessary to ensure accurate screening. In the mineral processing stage, a series of large - scale flotation machines or continuous - operation cyanidation plants are required. Automation control systems are also integrated into the production line to monitor and adjust the equipment operation in real - time, improving production efficiency and reducing labor costs.
Efficiency Enhancement and Cost Reduction
Optimizing the production line is not only about selecting the right equipment but also about proper operation and maintenance. Our company provides comprehensive after - sales services, including regular equipment maintenance, performance optimization, and operator training. By using high - quality wear - resistant parts for crushing equipment, we can extend the service life of the machines and reduce downtime. Additionally, our intelligent monitoring systems can predict potential equipment failures in advance, enabling timely maintenance and avoiding production interruptions.
An optimized gold ore beneficiation production line is the key to successful gold mining. With our advanced mining equipment and professional technical support, we are committed to helping our clients build efficient, reliable, and profitable gold ore beneficiation production lines, no matter the scale of the project.