In the world of industrial processing, the ability to efficiently break down materials into smaller, more manageable sizes is of utmost importance. Crushers with a high crushing ratio have emerged as essential tools for achieving this goal, enabling businesses to maximize their output and enhance overall productivity. This article delves into the significance of high crushing ratio crushers, explores the various types available, and highlights their key advantages and applications.
Understanding Crushing Ratio
The crushing ratio is a fundamental parameter that defines the effectiveness of a crusher. It is calculated by dividing the size of the largest feed particle by the size of the smallest product particle. A high crushing ratio indicates that the crusher can reduce large pieces of material to much smaller sizes in a single pass, minimizing the need for multiple stages of crushing and subsequent processing.
For example, if a crusher can take in rocks with a maximum size of 100 mm and produce particles as small as 5 mm, the crushing ratio would be 100/5 = 20. Crushers with high crushing ratios, often ranging from 10 to 60 or even higher depending on the type and design, are highly sought-after in industries where fine or ultra-fine particle sizes are required.
Types of Crushers with High Crushing Ratio
Jaw Crushers
Jaw crushers are widely used in primary crushing applications and are known for their high crushing ratio. They feature a fixed jaw and a movable jaw that work in tandem to compress and break the material. The large feed opening allows for the handling of big rocks and ores. As the material is fed into the crushing chamber, the movable jaw exerts a powerful squeezing force, reducing the size of the particles. Some advanced jaw crushers can achieve crushing ratios of up to 8:1 or more, making them suitable for initial reduction of large chunks of material in mining, quarrying, and construction industries.
Cone Crushers
Cone crushers are secondary or tertiary crushers that excel in producing fine and uniformly sized particles. They are designed to handle materials with high hardness, such as granite, basalt, and various ores. The crushing action in a cone crusher occurs between a mantle (movable cone) and a bowl liner (fixed cone). As the mantle gyrates within the bowl liner, the material is subjected to a combination of compression and shear forces, resulting in a high crushing ratio. Cone crushers can typically achieve ratios ranging from 3:1 to 10:1, depending on the specific model and the setting of the crusher. Their ability to produce consistent product sizes makes them ideal for applications where high-quality aggregates for construction or further processing in the mining industry are required.
Impact Crushers
Impact crushers are highly effective in achieving high crushing ratios, especially for materials with medium hardness, like limestone, dolomite, and some types of coal. These crushers operate by using the impact energy of a rapidly rotating rotor equipped with hammers or blow bars. When the material enters the crusher, it is struck by the high-speed rotor, which throws the particles against the breaker plates or anvils located within the crushing chamber. This impact causes the material to break into smaller pieces. Impact crushers can achieve extremely high crushing ratios, often in the range of 20:1 to 50:1 or even higher. Their ability to produce a cubic-shaped product makes them popular in the production of high-quality aggregates for concrete and asphalt, as well as in recycling applications where materials need to be reduced to specific sizes.
Hammer Crushers
Hammer crushers are designed to handle a variety of materials, including those with a high moisture content such as coal and clay. They feature a rotor with hammers that rotate at high speeds. As the material enters the crusher, it is struck by the hammers, which break it into smaller fragments. Hammer crushers are known for their high reduction ratio, which can be as high as 10:1 to 20:1 in some cases. Their relatively simple design and low power consumption make them suitable for use in mining operations, power plants, and other industries where large volumes of materials need to be crushed efficiently.
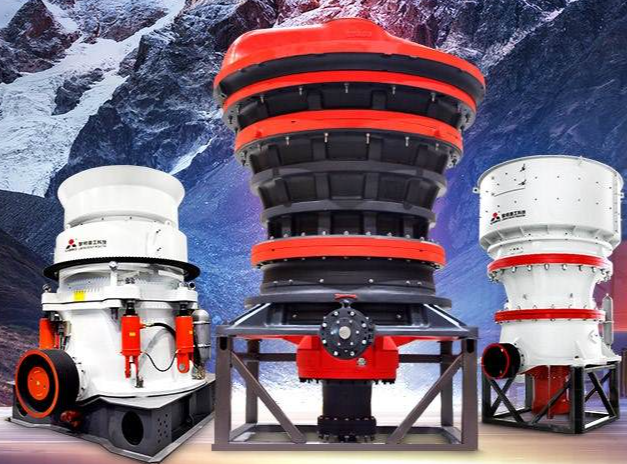
Advantages of High Crushing Ratio Crushers
Increased Productivity
High crushing ratio crushers enable businesses to process larger volumes of material in less time. With the ability to reduce the size of particles significantly in a single pass, fewer crushing stages are required, leading to a more streamlined production process. This not only saves time but also increases the overall throughput of the operation, allowing companies to meet higher production demands and potentially increase their market share.
Cost Savings
By minimizing the need for multiple crushing stages, high crushing ratio crushers can help reduce operational costs. Fewer crushers mean lower energy consumption, less wear and tear on equipment, and reduced maintenance requirements. Additionally, the reduction in the number of processing steps can lead to savings in labor costs and the cost of downstream processing equipment. For example, in a mining operation, if a high crushing ratio crusher can produce a product that is close to the final desired size, it can eliminate the need for additional grinding or re-crushing operations, resulting in substantial cost savings over the long term.
Better Quality Product
Crushers with high crushing ratios are often capable of producing a more uniform and consistent product size. This is particularly important in industries such as construction, where the quality of aggregates directly affects the strength and durability of concrete and asphalt. A high-quality product with a narrow particle size distribution can lead to better performance in downstream applications, reducing the risk of defects and ensuring a more reliable end product. In addition, the ability to produce fine or ultra-fine particles can open up new opportunities for businesses in industries such as pharmaceuticals, ceramics, and advanced materials, where precise particle sizes are crucial for product functionality.
Applications of High Crushing Ratio Crushers
Mining
In the mining industry, high crushing ratio crushers play a vital role in the extraction and processing of ores. They are used to break down large chunks of rock and ore into smaller sizes suitable for further beneficiation processes such as grinding, flotation, and leaching. Whether it's extracting valuable metals from copper, gold, or iron ores, or processing non-metallic minerals like limestone and quartz, crushers with high crushing ratios help improve the efficiency of ore processing, increase the recovery of valuable minerals, and reduce the overall cost of production.
Construction
The construction industry relies heavily on high-quality aggregates for the production of concrete, asphalt, and other building materials. Crushers with high crushing ratios are used to produce aggregates with the right size and shape characteristics. For example, in the production of concrete for high-rise buildings or infrastructure projects, the use of well-crushed aggregates can enhance the strength and workability of the concrete. Additionally, in road construction, high crushing ratio crushers are used to produce aggregates that meet the strict requirements for asphalt mixtures, ensuring the durability and performance of the roads.
Recycling
With the increasing emphasis on environmental sustainability, recycling has become an important industry. High crushing ratio crushers are used to break down a variety of waste materials, such as concrete, asphalt, and metal scraps, into smaller pieces for recycling and reuse. By reducing the size of these materials, crushers make it easier to separate and process different components, increasing the efficiency of the recycling process. For example, in a concrete recycling plant, crushers can break down old concrete slabs into smaller aggregates that can be used as a substitute for natural aggregates in new concrete production, reducing the demand for virgin materials and minimizing the environmental impact of construction activities.
Get on line help for your Crushing Needs